We are constantly striving to improve quality, working hard to deliver peace of mind and trust to our customers through the production of high-quality products.
Quality management system
Upon receiving your request, we acknowledge the receipt of the order documents
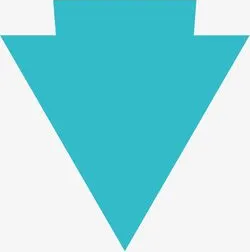
We arrange the materials through our certified material suppliers
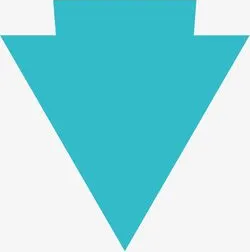
After confirming the materials and material certificates, we proceed with material cutting and pre-heat treatment (heat treatment certificate issuance)
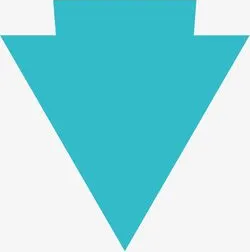
We organize the manufacturing process based on factors such as the number of parts and processing difficulty, and create a process flow document
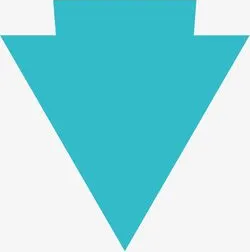
Each process is monitored by the responsible person, who conducts regular inspections of the part dimensions
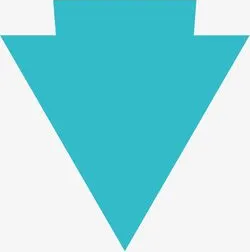
After completion of production, a third-party measurement is conducted, and the measured values are recorded in the self-inspection report
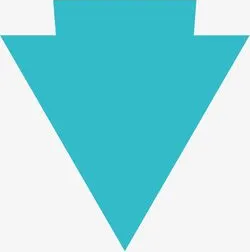
We send the inspection documents, including the self-inspection record, heat treatment record, material certificate, and reference photos, to the customer. After the customer reviews the documents, we obtain shipment approval
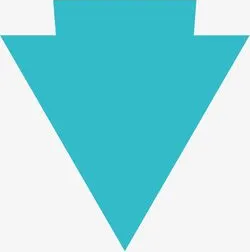
We package the parts and ship them to the customer's designated location
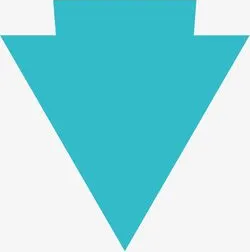
We receive feedback on the part inspection from the customer
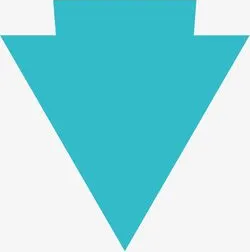
In case of any defects, we investigate the cause, consider measures to prevent recurrence, and report the findings to the customer
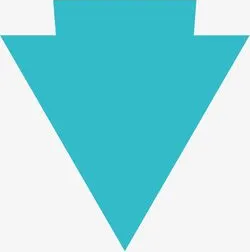
The recurrence prevention measures are compiled into a problem-solving manual, shared within the company, and applied to future production